Машины и оборудования для тепловой обработки кормов
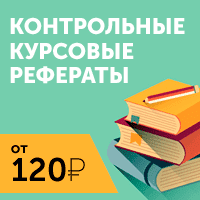
Тепловая обработка паром проводится с целью улучшения вкусовых и питательных свойств корма, а также уничтожения болезнетворных бактерий.
При тепловой обработке кормов необходимо выдерживать температурный и временный режимы с тем, чтобы корм хорошо пропарился, размягчился и прошёл гарантированную стерилизацию. После обработки корм охлаждают до температуры 40 ?С.
Обработанный корм должен быть сразу же скормлен животным, так как он не подлежит длительному хранению. Кроме того, остывший корм плохо поедается животными.
При использовании машин и оборудования для тепловой обработки кормов особое внимание необходимо уделять технике безопасности. Аппаратура водогрейных и паровых котлов должна быть в исправном состоянии, не допускается перегрев воды и пара, работа без защитных и предохранительных устройств.
При тепловой обработке корма энергия расходуется на нагрев корма, аппарата и на тепловой эффект производственного процесса (растворение кристаллов, испарение, поджаривание и др.), а также на покрытие потерь теплоты в окружающую среду.
Для получения пара с целью использования его для тепловой обработки кормов, нагрева воды, обогрева животноводческих помещений, стерилизации молочного оборудования используют котлы-парообразователи КВ-300М; КВ-300МТ; КТ-500; Д-721А; КЖ-1500 и др.
Котлы-парообразователи КВ-300МТ и КЖ-1500 работают соответственно на твёрдом и жидком топливе.
Котёл-парообразователь КЖ-1500 – жаротрубный, дымогарный, трёхходовый, выполнен на одной раме и имеет блочное исполнение основных сборочных единиц. Он состоит из котла в сборе, блока водоподводки и питания, горелки с топливной аппаратурой, арматуры, дымохода, электрошкафа. Работает котёл на жидком топливе, обслуживается одним человеком.
Современные котлы-парообразователи комплектуют системами автоматизации и контроля их работы, противонакипными магнитными устройствами (для умягчения воды).
Машины и оборудование для тепловой обработки кормов по способу обработки делятся на кормозапарники, запарники-смесители, кормозапарочные агрегаты, варочные котлы и сушильные установки, а по способу выполнения технологического процесса – на аппараты периодического и непрерывного действия.
В хозяйствах корма запаривают в запарочных чанах, цилиндрических ёмкостях и изготовленных из местных материалов ящиках.
Существенный недостаток кормозапарников – неравномерное запаривание корма. Для получения высококачественного и однородного корма, его необходимо запаривать одновременно со смешиванием. Поэтому наибольшее распространение получили запарники-смесители С-2, С-7, С-12, ЗС-6, варочный котёл ВК-1.
Запарник-смеситель кормов С-12 служит для приготовления кормовых смесей влажностью 65…80% из запаренных или сырых кормов, предназначенных для крупного рогатого скота, свиней и птицы.
Рабочий объём запарника-смесителя – 12 м3 , что позволяет запаривать и смешивать как сочные корма, так и смеси из грубых стебельчатых кормов. Грубые корма перед запариванием измельчают до частиц размером 50 мм.
При работе смесителя лопасти одного вала перемешивают корм в сторону привода, а лопасти другого – к выгрузной горловине.
Пар подводится к парораспределителю с двух сторон внизу корпуса.
Запарник-смеситель кормов С-12:
- крышка смесителя;
- щит;
- система управления шнеком и задвижкой;
- зубчатые колёса;
- редуктор привода;
- натяжное устройство цепной передачи;
- натяжное устройство;
- левый
- и правый лопастные валы;
- парораспределитель;
- система управления парораспрееделителя.
Производительность при механизированной загрузке на приготовлении кормосмесей составляет: с запариванием – 5 т/ч, без запаривания – 10 т/ч. Производительность шнека при выгрузке кормосмесей – до 40 т/ч.
Запарники-смесители С-2, С-7, ВК-1 по конструкции аналогичны запарнику –смесителю С-12. В процессе эксплуатации запарники-смесители обязательно очищают и промывают от остатков кормов, которые удаляются из корпуса запарника самотёком.
Кормозапарочные агрегаты служат для подготовки кормов и кормовых смесей. Они обычно совмещают несколько технологических операций.
Картофелезапарочный агрегат АЗК-3 служит для мойки, измельчения и запаривания картофеля, а также для отделения примесей. Он может использоваться самостоятельно при закладке на силос запарного картофеля или в сотаве комплектов оборудования кормоцехов для приготовления кормовых смесей на свиноводческих фермах. Производительность при запаривании картофеля составляет 3 т/ч.
Кормоприготовительный агрегат ЗПК-4 используют для мойки, запаривания и разминания картофеля на свиноводческих фермах.
Технологический процесс кормоприготовительного агрегата следующий. Подлежащий обработке картофель подают в мойку 3 (см. схему), где он промывается и шнеком 5 направляется на распределительное устройство 9, равномерно укладывающее картофель по всему сечению запарочного чана 10. Пар подаётся через паровой коллектор 11. Запаренный картофель выгрузным шнеком 15 продавливается через ножи 14 и поступает к мяльному шнеку 13, который измельчает и выгружает приготовленную массу.
Агрегат работает с ковшом-транспортёром ТК-3 для подачи картофеля и парообразователем типа КВ-300М.
Производительность запарника 1000 кг/ч, мощность электродвигателя 4,4 кВт.
Схема кормоприготовительного агрегата ЗПК-4:
- камнесборник;
- активатор;
- мойка;
- рукоятка заслонки камнесборника;
- шнек;
- водопровод;
- электродвигатель;
- привод;
- распределительное устройство;
- запарочный чан;
- паровой коллектор;
- кожух шнека;
- мяльный шнек;
- ножи;
- выгрузной шнек;
- конденсаторная труба;
- электродвигатель;
- редуктор;
- паропровод;
- вентиль.
Источник
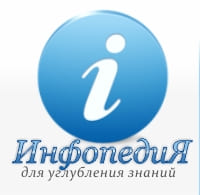
Мы поможем в написании ваших работ!
Мы поможем в написании ваших работ!
Мы поможем в написании ваших работ!
ЗНАЕТЕ ЛИ ВЫ?
Цель работы: изучить конструкцию и технологический процесс машин для смешивания и тепловой обработки кормов.
Заключительным этапом приготовления полнорационных кормовых смесей является процесс смешивания. Под смешиванием будем понимать процесс равномерного распределения частиц компонентов корма в общем его объёме для получения однородной кормовой смеси. Машины, в которых осуществляется процесс смешивания называются смесителями, а их рабочие органы – мешалками. Смесители классифицируются по следующим основным признакам:
– по характеру процесса: порционного (периодического) и непрерывного действия с вертикальным или горизонтальным расположением рабочих органов.
– в зависимости от вида животных и используемых компонентов кормов: для приготовления сухих сыпучих, рассыпных влажных и жидких кормовых смесей;
– по конструкции рабочих органов мешалок: лопастные, шнековые и ленточные для сыпучих кормов; пропеллерные, турбинные и лопастные для жидких кормов;
– по частоте вращения они могут быть тихоходные и быстроходные.
Смеситель С-3,0
Устройство. Смеситель С-3.0 –периодического действияпредназначен для приготовления кормовых смесей на животноводческих и птицеводческих фермах влажностью 60…80% из измельченных корнеклубнеплодов, зеленой массы, грубых и концентрированных кормов, с введением дополнительных ингредиентов. Предусмотрена возможность тепловой обработки как компонентов так и самой кормой смеси, пар подаётся под давлением 60 кПа (0,6 атм.).
Смеситель С-3.0 (рис. 1 а) состоит из корпуса 1, который служит ванной для запаривания и смешивания кормов. В верхней части смесителя установлены две оросительные трубы, служащие для подачи воды в корпус смесителя. К нижней части корпуса приварены трубы парораспределительной системы 7 для подвода пара в смеситель. Основными рабочими органами являются две лопастные мешалки 12, 16, с закрепленными на каждом валу шестью лопастями 14. При запаривании и перемешивании соломистой сечки на каждый вал устанавливаются только по три лопасти. Сверху смесителя установлен загрузочный люк 11 и смотровой люк 10. Приготовленная смесь выгружается из смесителя при открытой клиновой задвижки 23 шнеком 15.
Технологический процесс. Вначале в смеситель заливают воду (или раствор) по подведенному водопроводу (рис. 1 б). Количество подаваемой воды рассчитывается с учётом влажности исходных компонентов и требуемой влажности приготовляемой кормосмеси. При этом задвижка выгрузного шнека должна быть плотно закрыта. В первую очередь в смеситель подаются корма, которым нужна тепловая обработка. Для перемешивания компонентов мешалки включают при заполнении смесителя на 1/3 объёма. Мешалки работают таким образом, что лопасти правой мешалки активно перемешают корм в стороны привода, а левой в сторону выгрузной горловины, обеспечивая активное перемешивание массы в плоскости лопастей.
Рис. 1. а) Смеситель-запарник С-3.0: 1 – корпус; 2 – кронштейн крепления шкафа управления; 3 – шкаф управления; 4 –рычаг; 5 – приводная станция; 6 – ограждение; 7 – водопровод; 8 – манометр; 9 –ограничитель; 10 – смотровой люк; 11 – загрузочный люк; 12, 16 – валы; 13, 14 – лопасти; 15 – выгрузной шнек; 17 – парораспределительный трубопровод; 18, 19 – паропровод; 20 – тяга; 21 – лестница; 22 – рычаг; 23 – клиновая задвижка. б) Схема смесителя-запарника C-12: 1 – корпус; 2 – загрузочный люк; 3 – шиберная задвижка; 4 – деревянные крышки; 5 – тяга; 6 – выгрузная горловина; 7 – лопастные мешалки; 8 – труба для подвода пара; 9 – выгрузной шнек.
При необходимости процесс запаривания происходит в течение 50…70 мин под давлением пара 58,8 кПа (0,6 атм.) при температуре 90…95оС. После приготовления основных компонентов в смеситель подаются дополнительные ингредиенты, которым не требуется тепловая обработка, например – жидкие кормовые дрожжи, меласса и т.п. При приготовлении кормосмесей без запаривания все компоненты можно подавать одновременно. Время перемешивания в этом случае 10-15 мин.
Выгрузка кормов из смесителя производится шнеком при поднятом клиновом затворе и работающих мешалках.
Источник
Агрегат работает с ковшом-транспортером ТК-3 для подачи картофеля и парообразователем типа КВ-300М. Производительность запарника 1000 кг/ч, мощность электродвигателя 4,4 кВт.
Агрегат для приготовления заменителя молока АЗМ-0,8 предназначен для приготовления искусственного молока из сухих комбикормовых смесей, обрата, биостимуляторов, растительных и животных жиров, рыбьего жира, сахара, соли, мела и других компонентов. Искусственное молоко выпаивают телятам при помощи установки УВТ-20.
Агрегат АЗМ-0,8 состоит из бункера 1 (рис. 8.4), шнека 2, смесителя 3, бачка 4, насоса-эмульсатора 6 с фильтром 5, пульта управления, электропривода и соединительных трубопроводов для подачи воды и пара.
Рис. 8.4. Технологическая схема агрегата для приготовления молока A3M-0,8:
1 — загрузочный бункер; 2 – шнек; 3 – смеситель; 4 — бачок; 5 – фильтр; 6 — насос-эмульсатор
Технологический процесс агрегата протекает так. В бункер 1 загружают сухие компоненты, которые вертикальным шнеком 2 подаются в бак смесителя 3. В этот же бак по системе трубопроводов заливают воду, обрат и другие жидкие компоненты, которые обрабатывают паром при температуре 85 … 90 °С. Все компоненты тщательно перемешивают вертикальной мешалкой, затем охлаждают до 55 … 60 °С, пропуская через воздушную рубашку смесителя холодную проточную воду. После охлаждения проводят эмульсирование смеси. Кормовая смесь через фильтр 5 вместе с жирами из бачка 4 поступает в насос-эмульсатор 6, который дробит и превращает смесь в тонкодисперсную эмульсию. Эмульсия прокачивается в бак-смеситель. Прокачка длится 15 … 20 мин, после чего смесь охлаждают до 35 … 38 °С. Продолжительность приготовления заменителя молока составляет 3,5 ч, рабочая вместимость смесителя 800 л.
Поджаривание зерна позволяет повысить усвояемость крахмала, уничтожить вредные микроорганизмы, улучшить вкусовые качества. Перед поджариванием зерно намачивают до набухания, затем высыпают на металлические листы и нагревают до приобретения зерном светло-коричневого цвета. Хорошо поджаренное зерно делается хрупким и имеет приятный запах, его скармливают телятам.
Сушку фуражного зерна на комбикормовых заводах и кормоцехах проводят с целью его сохранения, когда влажность зерна выше 14 … 15 %. Для сушки применяют сушилки: барабанные СЗПБ-2,0, СЗСБ-4,0, СЗСБ-8,0, а также шахтные СЗШ-16,0, СЗШ-8,0 и передвижные ЗСПЖ-8.
8.2. Вспомогательное оборудование отделений, цехов и заводов
для приготовления кормовых смесей
Наряду с измельчителями, дробилками, запарниками, сушилками, грануляторами и другими машинами для выполнения основных технологических операций в комплект технологического оборудования отделений, кормоцехов и комбикормовых заводов входит большая группа вспомогательного оборудования, которое используют для объединения отдельных машин в технологические линии, равномерной загрузки машин, смешивания, транспортировки, выгрузки и хранения кормов. К числу вспомогательных машин и оборудования относят питатели, дозаторы, смесители, бункера-накопители, транспортирующие устройства и др.
Питатели предназначены для создания определенного запаса кормов и подачи их на дальнейшую обработку.
Шнековый питатель концентрированных кормов ПК-6,0 применяется в линиях концентрированных кормов. Он состоит из горизонтального выгрузного и вертикального подающего шнеков, установленных под углом 90о. Производительность питателя до 10 т/ч.
Транспортеры-питатели ТК-5Б и ТК-5 применяют для приема корнеклубнеплодов из автотранспорта и подачи их в мойки-измельчители. Производительность питателей — 5 т/ч, объем приемного бункера — 10 м3.
Питатель ПЗМ-1,5 используют для приема измельченной зеленой массы или силоса. Питатель входит в комплект оборудования типа АВМ. Он состоит из приемного бункера, транспортера, блока битеров, выгрузного шнека и наклонного выгрузного транспортера с разравнивающим битером.
Питатель КТУ-10 с электроприводом применяют для дозированной подачи зеленой массы и грубых кормов.
Питатель ПСМ-10 предназначен для приема, хранения и подачи сенной муки в кормоцех и устанавливается в нижней части бункера-хранилища. Он состоит из рамы, приводной станции, кожуха и выгрузного окна. Из питателя сенная масса подается скребковым транспортером на транспортер линии кормоприготовления. Производительность питателя составляет 30 … 35 м3/ч. Установленная мощность электродвигателя 1,5 кВт.
Накопители-питатели технологических линий кормоцехов (рис. 8.5) осуществляют, как правило, дозированную подачу компонентов. Поэтому они снабжены активными рабочими органами – шнеками, битерами, транспортерами или их сочетаниями. При этом в зависимости от физико-механических свойств кормов подача их к рабочим органам возможна самотеком.
Основные параметры накопителей-питателей (полезный объем, конфигурация, размер выпускного отверстия и способ выгрузки) определяют в зависимости от вида корма, производительности и режима работы технологической линии – порционное или непрерывно-поточное смешивание компонентов, наличие дополнительной , например механической или влаготепловой, обработки, а так же по технико-экономическим показателям.
Рис. 8.5. Технологические схемы накопителей-питателей:
а – с самотечным поступлением концентратов зерна; б, в, г – с принудительной подачей грубых кормов, силоса, зеленой массы
Дозаторы служат для дозирования по массе и объему компонентов кормов и кормовых смесей.
Объемное дозирование осуществляют в основном шнековыми (рис. 8.6) питателями, установленными в бункерах под углом от 0 до 45°, барабанными и тарельчатыми рабочими органами. Объемное дозирование приемлемо при 2-3 смешиваемых компонентах и условий, что составная часть рецепта одного из низ не должна быть менее 5%, т.к. отклонение компонентов при объемном дозировании может достигать 10-15%.
Рис. 8.6. Технологические схемы объемных дозаторов:
а — шнековые горизонтальные; б — шнековые наклонные; в — барабанные; г — тарельчатые
Весовое дозирование применяют при большом числе компонентов (до 10 и более) и дозировании компонентов, составляющих менее 3% смеси. Для этого в простейших случаях используют обычные весы, а в комбикормовом производстве – специальные весы-дозаторы.
Процесс дозирования может быть непрерывным (приготовление смесей из сухих сыпучих кормов) и порционным (приготовление смесей из самых разнообразных кормов).
Непрерывное дозирование обеспечивает ленточные, шнековые, весовые автоматические, барабанные и тарельчатые дозаторы (рис. 8.7).
Рис. 8.7. Схемы дозаторов кормов:
а — объемного порционного; б — объемного ленточного; в — объемного шнекового; г — массового (весового) автоматического непрерывного действия; д — объемного барабанного; е — объемного тарельчатого; 1 — бункер; 2 — заслонка с механизмом управления; 3 — ленточный или шнековый транспортер; 4 — датчик весов; 5 — балансир весов; 6 — командный аппарат; 7 — барабан; 8 – корпус; 9 – скребок; 10 — манжета; 11 — диск
Порционные дозаторы объемного дозирования имеют тарировочные емкости. Для дозирования по массе применяют обычные весы или весы-дозаторы.
Дозаторы должны обеспечивать необходимую точность дозирования. Погрешность дозирования по массе при наибольшей нагрузке на весовые аппараты допускается ± 2 %, а для объемных дозаторов ±0,1 … 1,5 % в зависимости от содержания ингредиентов в общей массе кормовой смеси. При дозировании травяной муки отклонения не должны превышать ±0,5%.
Бункер-дозатор БДК-Ф-70-20 используют для дозирования стебельчатых кормов в поточных линиях кормоцехов. Он состоит из емкости с подающим и выгрузным транспортерами с дозирующим устройством. Вместимость бункера 20 м3, диапазон дозирования от 5 до 20 т/ч.
Шнековый дозатор ДС-15 и барабанный дозатор ДП-1 служат для дозирования корнеплодов и зеленых кормов. Тарельчатые дозаторы ДТ, ДТК, МТД-ЗА и другие применяют в линиях концентрированных кормов для дозирования соли, мела, обогатительных смесей. Они состоят из бункера, выпускной трубы, ворошилки, тарельчатого диска, ножа сбрасывателя и механизма регулирования. Корм поступает сначала в бункер, а из него на тарельчатый диск, с которого равномерно сбрасывается в выпускной лоток. Производительность тарельчатых дозаторов от 30 до 750 кг/ч.
Дозатор комбикормов ДК-10 представляет собой бункер 3 (рис. 8.8) вместимостью 0,5 м3. В средней части бункер цилиндрический, а в нижней и верхней — в виде усеченного конуса. В каждой части бункера установлены датчики уровня 8, 9, 11, а вверху и в середине имеются смотровые окна 2 и 4. В загрузочной горловине 7 установлена сетка 6 для улавливания посторонних примесей. Дозирующая часть находится в нижней части бункера. Производительность при дозировании комбикорма — до 10 т/ч.
Тарельчатый дозатор ДДТ и дозатор комбикормов ДК-100 также предназначены для объемного дозирования концентрированных кормов и комбикормов. Автоматические весы ДМ-100-2 с погрешностью ±0,1 % используют для порционного взвешивания концентрированных кормов.
Рис. 8.8. Дозатор комбикормов ДК-10:
1, 14 — исполнительные механизмы; 2, 4 — смотровые окна; 3 — бункер; 5 – люк; 6 — сетка; 7 — приемная горловина; 8, 9, 11 — датчики уровня; 10 — разгрузитель; 12 — шкала; 13 — щелевое дозирующее устройство; 15 — электромагнит 16 – дозирующая заслонка; 17 – рабочая заслонка; 18 — прутковая ворошилка
Для дозирования и внесения воды, химических растворов и жидких кормовых добавок в кормоприготовлении применяют дозаторы-мерники, объемные счетчики, дозировочные насосы, которые оборудуют распылителями, и другие приспособления.
Смесители (рис. 8.9) разделяют так: по назначению — для сухих, жидких и полужидких кормов; по способу выполнения процесса — непрерывного и периодического действия; по расположению рабочего органа — горизонтальные и вертикальные; по форме рабочего органа — шнековые, лопастные, барабанные и пропеллерные.
Смесители выполняют заключительную операцию приготовления кормов. Кроме запарников-смесителей, агрегатов для смешивания грубых кормов и приготовления заменителя молока промышленность выпускает смесители СК-10, С-25, С-30, 2СМ-1, СМ-1,7, СМК-0,5 и др. Смеситель СК-10 используют для получения кормовых смесей и подачи их на выгрузной транспортер. Его производительность — 10 … 11 т/ч, продолжительность смешивания — 3 … 7 мин.
Смеситель С-30 предназначен для смешивания грубых кормов, силоса, сенажа и корнеклубнеплодов. Его производительность — 25 т/ч.
Смеситель непрерывного действия С-25 применяют для поточного механизированного приготовления влажных полнорационных кормовых смесей для свиней. Он состоит из корпуса, рабочих органов и привода. Рабочие органы (два лопастных вала) приводятся в действие от двигателя мощностью 5,5 кВт. Производительность машины до 25 т/ч.
Рис. 8.9. Схемы кормосмесителей:
а — шнекового горизонтального непрерывного действия; б — шнеково-лопастного горизонтального непрерывного действия; в — шнекового вертикального периодического действия; г, д — лопастных периодического действии; е — барабанного периодического действия; ж — пропеллерного непрерывного действия.
Смесители СМ-1,7 и СМК-0,5 служат для приготовления водного раствора меласы с карбамидом. Первые состоят из металлической емкости 1 (рис. 8.10) с лопастными рабочими органами, цистерны 3 вместимостью 5 м3 для подогрева и разжижения мелассы, трубопроводов 2 и 4 для подачи горячей воды, мелассы и отбора готовой смеси, шестеренчатого насоса, электрошкафа и привода. Уровень корма в емкости 1 контролируют с помощью указателя, смонтированного на торцевой части емкости. Производительность смесителя 1,8 т/ч, время приготовления смеси 6 … 8 мин.
Бункера-накопители предназначены для накапливания и хранения кормов в кормоцехах и животноводческих помещениях. По форме они могут быть прямоугольными с нижней частью в виде усеченной пирамиды или круглыми с нижней частью, изготовленной в виде усеченного конуса. В нижней, части бункеров монтируют выгрузные транспортеры шнекового или скребкового типа. Бункера-накопители изготовляют из листового железа, бетона или дерева.
Рис. 8.10. Смеситель мелассы СМ-1,7:
1 — емкость; 2 — трубопроводы; 3 — цистерна для хранения и подогрева мелассы; 4 — трубопровод для выдачи готовой смеси.
Бункер БСК-10 применяют для хранения концентрированных кормов. Он оборудован спирально-винтовым транспортером с тремя задвижками. Угол наклона транспортера в процессе установки можно менять от 15 до 30°. Производительность транспортера 2,1 т/ч. Рабочая вместимость бункера — 9 м3.
Бункер БСК-25 используется для хранения сухих концентрированных кормов и сыпучих смесей. Он загружается пневматическим способом путем соединения пневмотрубопроводом с автокормовозом АСП-25. Выгружают корма из бункера при помощи двух транспортеров производительностью 15 т/ч; вместимость бункера 25 м3.
Комплекты оборудования ОНК-1,5 и ОНК-3 производительностью соответственно 1,5 т/ч и 3 т/ч используют для кратковременного накопления и хранения гранулированной травяной муки или брикетов в технологических линиях по производству прессованных кормов. Комплекты включают в себя резервуары-накопители, конвейер, нории и щиты управления.
Транспортирующие устройства — транспортеры, шнеки и нории предназначены для транспортировки кормов, объединения кормоприготовительных машин в технологические линии, а также выгрузки кормов в кормовозы и раздатчики.
По типу рабочих органов транспортеры подразделяют на ленточные, шнековые, скребковые, ковшовые, цепочные и пневматические, шнеки и нории.
Ленточные транспортеры ТЛС-30, ТЛР-30, ТЛС-70 применяют для транспортировки измельченного сенажа, силоса, сена и соломы. Ленточные транспортеры ЛТ-6 и ЛТ-10 подают сыпучие корма. Рабочий орган такого транспортера — прорезиненная лента с резиновыми скребками. Лента натягивается на два концевых барабана и поддерживается роликами. Один из концевых барабанов приводится в движение от электродвигателя. Производительность транспортеров от 30 до 70 т/ч.
Транспортеры корнеклубнеплодов ТК-5 и ТК-5Б используют для подачи корнеклубнеплодов из хранилищ или бункеров-накопителей в транспортные средства, кормораздатчики или кормоприготовительные машины. Основные сборочные единицы транспортеров — горизонтальные шнековые питатели, приводная станция, наклонный скребковый транспортер. Производительность транспортеров 6 т/ч. Мощность электродвигателей горизонтального питателя и наклонного транспортера — 1,5 кВт.
Скребковые транспортеры TC-40G и ТС-40М предназначены для перемещения измельченной зеленой массы, травяной муки на технологическую линию кормоцехов, а также для подачи готовой кормовой смеси влажностью 65 … 80 % от смесителя к кормораздатчику. Основные сборочные единицы транспортеров — приводная, промежуточная и концевая секции, полотно, ведущий и ведомый валы. Полотно транспортера представляет собой две параллельные втулочно-роликовые цепи, соединенные скребками. Производительность 40 м3/ч, привод от электродвигателей мощностью 1,5 кВт у транспортера ТС-40С и 3 кВт у ТС-40М.
Ковшовый транспортер ТК-3 служит для подачи картофеля и других корнеклубнеплодов из приемников в агрегат ЗГЖ-4 или другие кормоперерабатывающие машины. Он состоит из рамы, привода и цепи с ковшами, смонтированной на двух валах. Верхний вал приводится в движение от электродвигателя мощностью 1,5 кВт. Производительность 3 т/ч.
Цепочные транспортеры ЦТ-12 и ЦТ-30 предназначены для транспортировки концентрированных кормов. Они состоят из приводной станции, секций с люком, секций с шибером и натяжной станции. Рабочий орган — втулочно-роликовая цепь с погружными скребками. Транспортеры могут комплектоваться различным набором секций с люком и секций с шибером, цилиндрическим или червячным редуктором приводной станции. Производительность транспортеров ЦТ-12 и ЦТ-30 соответственно составляет 12 и 30 т/ч, максимальная мощность электродвигателя 3 кВт, максимальная длина 60 и 30 м.
Для подачи в хранилища тюкованного сена и соломы применяют цепочный транспортер тюков ТТ-4 производительностью 4…12 т/ч.
Пневматический эжекторный передвижной транспортер ТПЭ-102А используют для погрузки измельченного сена и соломы в хранилища. Корм, загружаемый в бункер транспортера, под действием разрежения попадает в промежуточную камеру, а затем воздушным потоком, создаваемым вентилятором, транспортируется по трубопроводу к месту хранения или переработки. Производительность транспортера до 10 т /ч.
Шнеки, загрузочный ШЗС-40 и выгрузной ШВС-40, служат для загрузки измельченных корнеклубнеплодов, травяной муки, концентрированных кормов и зеленой массы в смесители и выгрузки готовой смеси. Производительность шнеков 40 т/ч.
Наклонный двухвальный ШНД-25 и горизонтальный двухвальный ШГД-25 шнеки используют для перемещения кормовых смесей грубых, сочных и концентрированных кормов в технологических линиях кормоцехов. Рабочие органы представляют собой два параллельно расположенных шнека диаметром 200 мм, вращающихся навстречу друг другу. Производительность шнеков 40 т/ч.
Нории НЦГ-10, НЦГ-20 служат для вертикального перемещения травяной муки, комбикормов, зерна, гранул и других сыпучих материалов в кормоцехах и на комбикормовых заводах. Производительность НЦГ-10 составляет 10 т/ч, а НЦГ-20 — 20 т/ч при транспортировке зерна. Нории могут поднимать продукт на высоту до 30 м и более.
Источник