Техническое обслуживание машин для измельчения грубых и сочных кормов
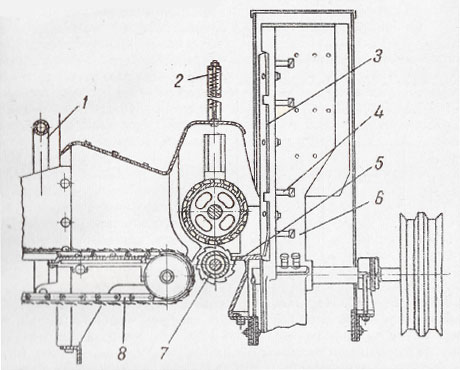
Доставка сельхозтехники и запасных частей, оросительных систем, насосов во все города России (быстрой почтой и транспортными компаниями), так же через дилерскую сеть: Москва, Владимир, Санкт-Петербург, Саранск, Калуга, Белгород, Брянск, Орел, Курск, Тамбов, Новосибирск, Челябинск, Томск, Омск, Екатеринбург, Ростов-на-Дону, Нижний Новгород, Уфа, Казань, Самара, Пермь, Хабаровск, Волгоград, Иркутск, Красноярск, Новокузнецк, Липецк, Башкирия, Ставрополь, Воронеж, Тюмень, Саратов, Уфа, Татарстан, Оренбург, Краснодар, Кемерово, Тольятти, Рязань, Ижевск, Пенза, Ульяновск, Набережные Челны, Ярославль, Астрахань, Барнаул, Владивосток, Грозный (Чечня), Тула, Крым, Севастополь, Симферополь, в страны СНГ:Киргизия, Казахстан, Узбекистан, Киргизстан, Туркменистан, Ташкент, Азербайджан, Таджикистан.
Наш сайт не является публичной офертой, определяемой положениями Статьи 437 (2) ГК РФ., а носит исключительно информационный характер. Для получения точной информации о наличии и стоимости товара, пожалуйста, обращайтесь по нашим телефонам. В случае копирования, использования любого материала находящегося на сайте www.newtechagro.ru, активная ссылка обязательна, в случае печати – печатная ссылка. Копирование структуры сайта, идей или элементов дизайна сайта строго запрещено.
Права на все торговые марки, изображения и материалы, представленные на сайте, принадлежат их владельцам.
Машины для измельчения грубых кормов
Соломосилосорезки служат для измельчения соломы, сена, трав и силосной зелени. По конструкции режущего рабочего органа их разделяют на дисковые и барабанные. Резание происходит при защемлении продукта между подвижным ножом и неподвижной противорежущей пластиной.
Измельчаемый продукт подается транспортером к питающим вальцам, которые затягивают, прессуют и подают продукт к измельчающему устройству.
Соломосилосорезки РСС-6 и РСС-6А состоят из рамы, питающих вальцов, транспортера, режущего аппарата, передаточного механизма с системой управления и отводящих труб с дефлектором.
Рабочий орган машины — ротор с двумя ножами, имеющими криволинейную форму лезвия. Ножи крепятся к ротору в трех точках при помощи болтов. Положение лезвия относительно противорежущей грани пластины 5 (рис. 27) регулируют отжимными винтами 4. Механизм привода имеет шестеренчатые, цепные и шарнирную (к верхнему «плавающему» вальцу) передачи. Система управления выполнена в виде храповой муфты на шпонке короткого промежуточного вала. Муфта перемещается вдоль вала при помощи системы рычагов от ручной скобы, через которую управляют работой питающего механизма.
Для получения резки различной длины пользуются сменой пар шестерен в соответствии с таблицей 18.
Таблица 18.
Расчетная длина резки при установленных сменных парах шестерен
Число зубьев шестерен | Расчетная длина резки, мм | |
ведущей | ведомой | |
24 | 58 | 15 |
38 | 24 | 40 |
30 | 32 | 25 |
32 | 30 | 27 |
12 | 50 | 6 |
50 | 12 | 104 |
6 | 56 | 2 |
56 | 6 | 220 |
Соломосилосорезка РСС-6А оборудована приводом от собственного электродвигателя через клиноременную передачу, в отличие от РСС-6,0, имеющей плоскоременный привод от трактора.
Для мелкоизмельченного продукта РСС-6А оборудована циклоном, устанавливаемым на конце выводной трубы.
Подача продукта производится на высоту до 15 м при помощи лопаток, установленных на роторе машины. Обслуживают машину 3 – 4 человека.
Соломорезка РСС-6Б выполнена в стационарном и передвижном вариантах. Стационарный вариант с приводом от электродвигателя; передвижной — от вала отбора мощности тракторов серии МТЗ, на которые она навешивается. Крылач машины имеет прямые ножи, установленные на регулируемых кронштейнах. Дополнительно к питающим валикам машина оборудована коротким подпрессовывающим транспортером плавающего типа. Для контроля за подачей материала машина снабжена специальным прибором, определяющим степень ее загрузки. Машина имеет заточное приспособление. Выгрузной дефлектор кормопровода оборудован поворотным устройством. Высоту подачи до 8 м машина обеспечивает за счет лопастей, укрепленных на роторе. Машину обслуживают 2 – 4 человека.
Рис. 27. Соломосилосорезка РСС-6 (питающий и режущий механизм):
1 — скоба управлении; 2 — пружина подпрессовывающего вальца; 3 — нож; 4 — регулировочные винты; 5 — противорежущая пластина; 6 — лопасть крылача; 7 — нижний питающий валец; 8 — транспортер
Соломосилосорезка РСБ-3,5МЧ состоит из рамы, барабанного режущего аппарата, транспортера, питающих вальцов, передаточного механизма. Барабан имеет 6 ножей, поставленных на двух дисках под углом к образующей барабана. В средней части ножей находится регулировочное устройство для выравнивания зазора между лезвием и противорежущей гранью.
Величина зазора выбирается перестановкой противорежущей пластины по раме. Для нормальной работы машины величина зазора не должна превышать 0,5 мм. Длина резки 2, 8, 14, 20, 28 и 40 мм устанавливается путем перестановки сменных шестерен и снятием через один нож трех ножей с режущего барабана.
Управление машиной осуществляется при помощи кнопочного магнитного реверсивного пускателя на три позиции: «стоп», «рабочий ход» и «обратный ход», которым пользуются для, освобождения питающего механизма от посторонних предметов во время пуска и при забивании режущего аппарата, В таблице 19 приведена технологическая характеристика соломосилосорезок.
Технический уход за соломосилосорезками заключается в проверке и подтяжке креплений, натяжении цепных передач, смазке подшипников, переточке ножей, регулировках режущего и питающего устройств. Угол заточки ножей РСС-6 и РСС-6А — 12°, ножей РСБ-3,5МЧ — 16°. Нормальная острота лезвия 40 – 45 мк. При работе соломосилосорезок нужно следить, чтобы в машину не попали посторонние предметы. Нельзя очищать забившиеся вальцы руками или палками и т. п. Не рекомендуется находиться в плоскости вращающегося ротора. Продукт требуется подавать на транспортер ровным слоем.
Таблица 19.
Техническая характеристика соломосилосорезок
Показатели | РСС-6А | РСС-6Б | РСБ-3,5МЧ |
Производительность, т/час: | |||
на резке соломы | 1,8 | 2,0 | 0,8 |
на резке зелени | 7 | 10 | 3,5 |
Потребная мощность, квт | 7,5 | 17 | 3,5 |
Измельчитель грубых кормов ИГК-30А применяют для измельчения соломы в мякинообразную массу. Машина состоит из рамы, приемника, питающего и измельчающего устройств, приставного стола и отводящей трубы. Корм сбрасывают с приставного стола в приемник на вильчатый питатель, который подает продукт в зубчатый измельчитель, составленный ротором и неподвижным кольцом с укрепленными на них концентрическими рядами перекрывающихся штифтов-зубьев. Под действием воздушного напора и возникающей центробежной силы продукт отбрасывается к зубьям и перетирается.
Лопасти ротора обеспечивают транспортирование измельченной массы по трубе на расстояние до 7 м по вертикали и до 20 м по горизонтали. Машина не требует регулировок, обслуживают ее 1 – 2 человека. Привод машины от электродвигателя или от трактора осуществляется с помощью плоскоременной передачи. Требования к технике безопасности подобны требованиям к обслуживанию соломосилосорезок, т.е. нельзя продвигать корм в приемную камеру руками или вилами и т. д. Очищать камеру следует только после остановки машины. Производительность ИГК-30А — 3 т/час при потребной мощности 12 – 18 квт и 1000 оборотах ротора в минуту. Вес машины 1120 кг.
Источник
Цель работы: изучить конструкцию и технологический процесс машин для измельчения и обработки грубых и концентрированных кормов, корнеклубнеплодов.
Машины для измельчения грубых кормов
Для механического измельчения грубых кормов применяются измельчители, которые представляют собой большую группу машин с различными принципами действия измельчающих аппаратов. В настоящее время используют дисковые и барабанные режущие аппараты, штифтовые измельчающие устройства, роторно-молотковые механизмы.
Измельчитель ИКВ-Ф-5А (Волгарь-5)
Устройство.Измельчитель предназначен для равномерного измельчения всех видов сочных и грубых кормов: силоса, корнеклубнеплодов, бахчевых культур, любой зеленой массы, сена, соломы, веточного корма. Все перечисленные корма можно перерабатывать раздельно, а также в различной смеси. В этом случае наряду с измельчением происходит перемешивание кормов. Измельчитель предназначен для животноводческих, птицеводческих и звероводческих ферм и может быть использован на переработке продуктов при закладке комбинированного силоса в хранилища.
Рис. 1. Схема измельчителя кормов ИКВ-Ф-5А (Волгарь-5): 1 – приямок; 2 – транспортёр загрузки измельчённого корма; 3 – аппарат вторичного резания; 4 – нижнее окно корпуса; 5 – шнек; 6 – заточное устройство; 7 – режущий барабан; 8 – прессующий транспортёр; 9 – подающий транспортёр; 10 – электродвигатель.
Основные части измельчителя: рама; корпус; подающий и нажимной плавающий транспортер пластинчатого типа; режущий барабан первой ступени измельчения (частота вращения 725 мин-1) с шестью спиральными ножами и противорежущей пластиной; шнек; режущий барабан второй ступени (частота вращения 1000 мин -1) с девятью подвижными и неподвижными ножами; заточное приспособление, установленное на крышке корпуса; механизм привода (состоит из двухступенчатого цилиндрического редуктора с реверсом и клиноременных передач); пусковая и защитная аппаратура. Привод осуществляется от электродвигателя.
Технологический процесс. Подготовленный к измельчению корм укладывают ровным слоем на подающий транспортер 9, откуда он, подпрессованный транспортером 8, направляется к режущему барабану 7 первой ступени резания, где происходит предварительное измельчение до фракций 20…80 мм (рис. 1).
Измельчённая масса направляется шнеком 5 к аппарату вторичного резания 3, где корм подвижными и неподвижными ножами измельчается до фракций 2…10 мм. и выбрасывается через нижнее окно корпуса 4. Для удобства выгрузки кормов из под окна корпуса рекомендуется устроить приямок 1 с транспортером загрузки измельченного корма 2.
Измельчитель грубых кормов (ИГК-30Б)
Устройство. Измельчитель грубых кормов (ИГК-30Б)предназначен для измельчения сухих стебельчатых кормов (грубых кормов) с расщеплением их вдоль волокон. Применяется на фермах крупного рогатого скота. Промышленность выпускает измельчитель в двух исполнениях: ИГК-ЗОБ-1(навесной на трактор типа «Беларусь» с приводом от ВОМ) и ИГК-ЗОБ-II. (стационарный с приводом от электродвигателя).
Рис. 2. Технологическая схема измельчителя грубых: кормов ИГК-З0Б: 1 – дефлектор; 2 – регулируемый козырёк; 3 – диск; 4 – штифт; 5 – приёмная камера; 6 – прессующий транспортёр; 7 – питающий транспортёр; 8 – лопатка; 9 – ротор; 10 – лопасть ротора.
Измельчитель снабжен измельчающим аппаратом штифтового типа. Наличие в ИГК-30Б горизонтального 7 и прессующего 6 транспортеров облегчает загрузку машины и способствует увеличению ее производительности (рис. 2).
Технологический процесс. Корм, подлежащий измельчению, по транспортёру 7 (рис. 2) поступает к прессующему транспортёру 6 и направляется в приёмную камеру 5. До поступления в измельчающую камеру под действием собственной массы происходит отделение тяжелых примесей, которые выпадают через окно приемной камеры 5.
В измельчающей камере корм, проходя между штифтами 4 неподвижного и подвижного дисков 3 дробильной камеры измельчается (солома разрывается, расщепляясь вдоль и поперек волокон, длина резки соломы 30 мм) и далее воздушным потоком и лопатками 8 выбрасывается через дефлектор 1. Регулируемый козырёк 2 и механизм поворота позволяют равномерно распределить измельчённый корм по кузову транспортного средства. Для предотвращения распыливания корма транспортные средства должны быть оборудованы сетками.
Машины для обработки концентрированных кормов
В машинах для обработки концентрированных кормов используются следующие виды обработки исходного продукта: плющение, скалывание, размол или дробление при свободном ударе. Наиболее широкое применение нашло дробление свободным ударом, которое реализовано в молотковых дробилках. Простота устройства, высокая надёжность в работе, компактность установки обусловили возможность широкого их применения.
Наряду с этим молотковые дробилки обладают рядом недостатков: высокая энергоёмкость, неравномерность гранулометрического состава получаемого продукта, интенсивный износ рабочих органов.
В зависимости от организации рабочего процесса в рабочей камере различают дробилки открытого или закрытого типа.
По назначению дробилки могут быть специализированными (для дробления продукта одного вида) и универсальными. В зависимости от вида сепарации готового продукта они могут быть как решётные, так и безрешётные.
Дробилка молотковая КДМ-2,0
Устройство. Дробилка молотковая КДМ-2,0 предназначена для измельчения зерна и жмыха. Дробилка может применяться в кормоцехах, мельницах и кормоприготовительных отделениях при животноводческих фермах.
Кормодробилка молотковая КДМ-2,0 (рис. 3 а) состоит из рамы, бункера с двумя магнитными сепараторами, дробильной камеры с барабаном, циклона со шлюзовым затвором, фильтрующего рукава, вентилятора, электропривода и пускового оборудования.
Основной технологический процесс проходит в дробильной камере (рис. 3 б), которая состоит из чугунного корпуса 2 со вставными боковинами, несущих корпусов подшипников главного вала дробилки и задней стенки, выполненной в виде откидывающейся крышки 6. Внизу крышка дробильной камеры имеет окно, к которому на быстросъемных замках жестко крепят всасывающий трубопровод вентилятора 3.
Технологический процесс. Для получения необходимой фракции измельчения перед запуском дробилки необходимо открыть откидную крышку дробильного барабана и поставить соответствующее сменное решето. Для мелкого дробления в камеру дробилки вставляют решето с отверстиями – 4 мм, среднего – 6мм и крупного– 8мм. Величина подачи продукта в дробильную камеру регулируют заслонкой приёмного бункера, а загрузка машины контролируется амперметр-индикатором, показания которого не должны превышать 55-ампер.
Рис. 3. а) Дробилка молотковая КДМ-2,0: 1 – дробильная камера; 2 – вентилятор; 3 – шлюзовой затвор; 4 – циклон; 5 – фильтрующий рукав; 6 – бункер; 7 – привод.
б) Дробильная камера: 1 – дробильный барабан; 2 – корпус дробильного барабана; 3 – вставная выбросная горловина; 4 – решето сменное; 5 – выбросной люк дробильной камеры; 6 – крышка дробильной камеры; 7 – зарешетная полость; 8 – зерновой ковш; 9 – регулировочная заслонка; 10 – электродвигатель.
Из приёмного бункера зерно, проходя по наклонному днищу горловины, очищается магнитным сепаратором от металлических предметов и попадает в дробильную камеру, где под действием ударов молотков, дек и решета измельчается. Измельчённые частицы корма через отверстия решета поступают в зарешётное пространство, откуда отсасываются вентилятором и транспортируются в циклон. В циклоне, вследствие образовавшегося в нём интенсивного завихрения, происходит отделение воздуха от продукта, который через шлюзовой затвор порциями выдаётся в мешкотару, подвешенную к раструбу. Воздух, через обратный трубопровод, фильтрующий рукав и приёмный патрубок поступает обратно в дробильную камеру.
Дробилка безрешётная ДБ-5
Устройство. Дробилка безрешётная ДБ-5предназначена для измельчения различных видов фуражного зерна для животных и птицы. Выпускают в двух исполнениях: ДБ-5-1 – укомплектована самой дробилкой, загрузочным и выгрузным шнеками и шкафом управления. ДБ-5-2 – укомплектована только дробилкой и укороченным загрузочным шнеком.
Основные сборочные единицы дробилки крепятся к корпусу. В горловине корпуса установлены разделительная камера 2 и кормопровод 3 (рис. 4 а).
Рис. 4. а) Устройство ДБ-5: 1 – фильтр; 2 – разделительная камера; 3 – кормопровод; 4 –механизм управления заслонками; 5 – ведомый двухступенчатый шкив; 6 – скоба; 7 – рамка; 8 – бункер; 9 – ротор; 10 – рама; 11 – корпус; 12 – крышка откидная; 13 – втулочно-пальцевая муфта; 14 – электродвигатель; 15 – привод заслонки.
б) Технологическая схема дробилки ДБ-5: 1 – шнек загрузочный; 2 – бункер; 3 – камера дробильная; 4 – кормопровод; 5 –разделительная камера; 6 – дефлектор; 7 – возвратный канал; 8 – заслонка; 9 – окно прохода готовой продукции; 10 – шнек дробилки; 11 – козырек; 12 – рециркуляционный канал воздуха; 13 – фильтр; 14 – выгрузной шнек; 15 – датчики уровня; 16 –дополнительный шнек; 17 – деки; 18 – заслонка подачи; 19 – магнит.
Бункер имеет загрузочную и смотровую горловины. В нижней части бункера установлен привод заслонки 15, а на наклонной стенке – батарея постоянных магнитов для улавливания металломагнитных примесей. По вертикали в бункере установлены датчики нижнего и верхнего уровней зерна, посредством которых включается и отключается загрузочный конвейер.
Степень загрузки дробилки регулируют поворотом заслонки как от привода, так и вручную рычагом. При ручном управлении, контроль за загрузкой ведут по показаниям амперметра-индикатора. При установившемся заданном режиме рычаг фиксируют.
Технологический процесс. Зерно дополнительным шнеком 16 и загрузочным конвейером 1 подаётся в приёмный бункер дробилки, в котором размещены датчики уровня 15 (рис. 4 б). Верхний датчик останавливает поступление зерна в бункер, а нижний – включает конвейер в работу. Зерно из бункера через загрузочное окно, регулируемое заслонкой 18, проходит через магнит19 и циркулирующим по замкнутому контуру воздухом, подаётся в дробильную камеру 3.
Измельчённый продукт по кормопроводу 4 потоком воздуха выбрасывается на сепарирующее устройство, где разделяется на фракции. Готовый продукт поступает в разделительную камеру 5, откуда выгрузным шнеком подаётся в тару или на линию приготовления кормосмесей. Крупная фракция по возвратному кормопроводу направляется в дробильную камеру на повторное измельчение. В разделительной камере установлена специальная заслонка 8, при помощи которой измельчённый продукт предварительно разделяется на мелкую и крупную фракции.
Источник
Наиболее интенсивно изнашиваются рабочие органы: дробильные молотки, решета, режущие и противорежущие пластины, ножи, деки и др. Дробильные молотки. Износ рабочей грани дробильных молотков допускается не более 4 мм по высоте. В случае износа граней молотки переставляют для работы неизношенной стороной. Перед сборкой следует подобрать в комплект молотки, шайбы и оси по массе так, чтобы у диаметрально расположенных комплектов (всего 6 комплектов) разница в массе была не более 12 р. Изношенные отверстия в молотках развертывают и устанавливают оси увеличенного размера.
Решета. При затуплении острых кромок отверстий решет до радиуса более 2 мм их переставляют (четыре положения), используя неизношенные. В случае пробоин на решета ставят накладки от старых решет, используя газовую сварку. После ремонта решето должно иметь правильную форму и при установке входить в паз с усилием 70 … 80 Н.
Режущие Аппараты. Затупляются и повреждаются ножи и противорежущие пластинки, ослабляется крепление фланцев на диске, прогибается вал и изнашиваются подшипники.
Затупившиеся до толщины кромок более 0,6 мм лезвия ножей и противорежущих пластин затачивают до толщины 0,1 мм на абразивных кругах при обильном охлаждении. Углы заточки ножей дробилок типа ДКУ должны быть 24 … 26° (проверять шаблоном), у противорежущих пластин -60 … 61°.
Нож и детали его крепления после заточки устанавливают на прежние места для сохранения балансировки. Между ножом и противорежущей пластиной должен быть зазор 0,5 … 1,5 мм в зависимости от вида перерабатываемого корма. Этот зазор регулируют постановкой прокладок под кронштейн. В дробилках типа ДКУ нож устанавливают по отношению к плоскости диска под углом 2°, а противорежущие пластины под углом 15° к горизонтали с зазором 0,3 … 0,5 мм.
Зазор между режущим барабаном и противорежущей пластиной в измельчители кормов «Волгарь-5» должен быть в пределах 0,5 … 1 мм при разнице его по длине пластины не более 0,2 мм.
У ножей аппаратов вторичного резания изнашиваются торец и боковые грани. При толщине более 7 мм торцевые поверхности шлифуют до выведения следов износа. Если толщина боковых граней меньше 7 мм по всей их длине, газовой сваркой наплавляют слой сормайта № 1 (1,5 … 2 мм) и обрабатывают. Для ножей вторичного резания зазор должен быть 0,1 … 0,5 мм.
Углы заточки и ширина наплавленного слоя ножей: а и В — Универсальной и перспективной кормодробилок: б — соломосилорезки; Гид — измельчителей корнеклубнеплодов; Е — агрегата для приготовления кормов; ж— измельчителя «Волгарь-5,
Чтобы увеличить износостойкость ножей машин, измельчающих корма, рекомендуется их наплавить твердыми сплавами марка ПГС-27, ПГ-С1 и др. направленные ножи (рис.) в процессе работы самозатачиваются, и их износостойкость в 2 … 2,5 раза выше серийных. При использовании таких ножей повышается качество измельчения кормов и уменьшаются затраты энергии.
Измельчающие аппараты. У измельчителей грубых кормов ИГК-30, например, изнашиваются и деформируются лопасти, рожки, крыльчатки и зубцы измельчающего аппарата, нарушается его балансировка, поврежденные лопасти рихтуют или заменяют. Биение диска допускается не более 1,5 мм.
Закругленные до радиуса более 4 мм рабочие грани зубцов оттягивают кузнечным способом, нагревая до температуры 820 … 840 °С, и закаливают в воде при 40 … 50 °С на длине 15 … 20 мм от вершины. Крыльчатку и барабаны после ремонта статически и динамически балансируют. Допустимый дисбаланс 10 МН-м.
Матрица гранулятора. Изнашиваются внутренняя поверхность и поверхности отверстий для образования гранул со стороны входа массы травяной муки. Восстанавливают матрицы расточкой на увеличенный размер и гильзованием. Для расточки внутренней поверхности применяют резцы с металло-керамическими пластинками из гексанита Р. Гильзу готовят из стали 20, сверлят отверстия, используя матрицу в качестве кондуктора, а затем гильзу цементуют на глубину 1,2 … 1,5 мм и закаливают до твердости НКС 60 … 62. Гильзу фиксируют в матрице штифтами.
Детали механизмов подачи.
Характерные дефекты: выкраивание и поломка продольных рифов или зубьев вальцов, неисправности транспортеров, износ шестерен, валов и подшипников.
Поломанные продольные рифы, зубья вальцов и гребенки восстанавливают приваркой изготовленных и подогнанных рифов и зубьев.
Ремонт машин и механизмов для раздачи кормов и удаления навоза.
В мобильных машинах, таких, как агрегат типа АПК-Ю для приготовления комбинированных силосов, измельчитель-погрузчик силоса ПСН-1М, кормораздатчик ПТУ-10К, раздатчик-смеситель РС-5А и других, установлены детали, подобные аналогичным деталям рассмотренных машин. Дефекты типовых деталей машин аналогичны, и их восстановление выполняется, как показано в других разделах. При сборке машин и механизмов для раздачи кормов и удаления навоза натяжение цепей регулируют так, чтобы в случае приложения усилия 10 Н в середине пролета цепи ее отклонение было 25 … 40 мм.
В транспортерах ТВК-80А возможны поломки скребков, износ осей звеньев и отверстий в планках, разрывы цепи, соскакивание цепи с натяжкой звездочки из-за удлинения и перекосов оси натяжного вала, изгибы и скручивания валов и др.
Примерные сроки замены основных узлов и деталей транспортера ТСН-3,0Б
Детали | Допустимый износ, мм | Сроки замены деталей, ч |
Поворотная звездочка | 12-14 | 450-500 |
Ведущая звездочка | 5-5,5 | 900-1000 |
Натяжная звездочка | 12-14 | 1500-1800 |
Оси: | ||
Поворотной звездочки | 0,02 | 2200-2500 |
Натяжной звездочки | 0,02 | 3000-3600 |
Тяговая цепь | 4500-5000 | |
Редуктор | 5000-5800 |
Источник