То и ремонт машин и аппаратов для приготовления кормов
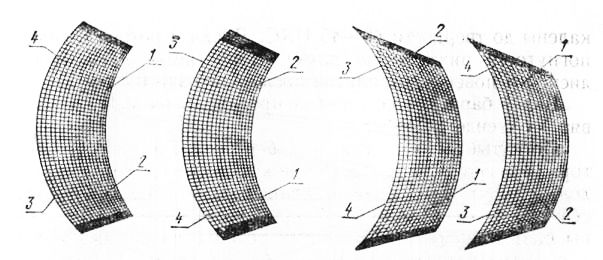
Наиболее интенсивно изнашиваются рабочие органы: дробильные молотки, решета, режущие и противорежущие пластины, ножи, деки и др. Дробильные молотки. Износ рабочей грани дробильных молотков допускается не более 4 мм по высоте. В случае износа граней молотки переставляют для работы неизношенной стороной. Перед сборкой следует подобрать в комплект молотки, шайбы и оси по массе так, чтобы у диаметрально расположенных комплектов (всего 6 комплектов) разница в массе была не более 12 р. Изношенные отверстия в молотках развертывают и устанавливают оси увеличенного размера.
Решета. При затуплении острых кромок отверстий решет до радиуса более 2 мм их переставляют (четыре положения), используя неизношенные. В случае пробоин на решета ставят накладки от старых решет, используя газовую сварку. После ремонта решето должно иметь правильную форму и при установке входить в паз с усилием 70 … 80 Н.
Режущие Аппараты. Затупляются и повреждаются ножи и противорежущие пластинки, ослабляется крепление фланцев на диске, прогибается вал и изнашиваются подшипники.
Затупившиеся до толщины кромок более 0,6 мм лезвия ножей и противорежущих пластин затачивают до толщины 0,1 мм на абразивных кругах при обильном охлаждении. Углы заточки ножей дробилок типа ДКУ должны быть 24 … 26° (проверять шаблоном), у противорежущих пластин -60 … 61°.
Нож и детали его крепления после заточки устанавливают на прежние места для сохранения балансировки. Между ножом и противорежущей пластиной должен быть зазор 0,5 … 1,5 мм в зависимости от вида перерабатываемого корма. Этот зазор регулируют постановкой прокладок под кронштейн. В дробилках типа ДКУ нож устанавливают по отношению к плоскости диска под углом 2°, а противорежущие пластины под углом 15° к горизонтали с зазором 0,3 … 0,5 мм.
Зазор между режущим барабаном и противорежущей пластиной в измельчители кормов «Волгарь-5» должен быть в пределах 0,5 … 1 мм при разнице его по длине пластины не более 0,2 мм.
У ножей аппаратов вторичного резания изнашиваются торец и боковые грани. При толщине более 7 мм торцевые поверхности шлифуют до выведения следов износа. Если толщина боковых граней меньше 7 мм по всей их длине, газовой сваркой наплавляют слой сормайта № 1 (1,5 … 2 мм) и обрабатывают. Для ножей вторичного резания зазор должен быть 0,1 … 0,5 мм.
Углы заточки и ширина наплавленного слоя ножей: а и В — Универсальной и перспективной кормодробилок: б — соломосилорезки; Гид — измельчителей корнеклубнеплодов; Е — агрегата для приготовления кормов; ж— измельчителя «Волгарь-5,
Чтобы увеличить износостойкость ножей машин, измельчающих корма, рекомендуется их наплавить твердыми сплавами марка ПГС-27, ПГ-С1 и др. направленные ножи (рис.) в процессе работы самозатачиваются, и их износостойкость в 2 … 2,5 раза выше серийных. При использовании таких ножей повышается качество измельчения кормов и уменьшаются затраты энергии.
Измельчающие аппараты. У измельчителей грубых кормов ИГК-30, например, изнашиваются и деформируются лопасти, рожки, крыльчатки и зубцы измельчающего аппарата, нарушается его балансировка, поврежденные лопасти рихтуют или заменяют. Биение диска допускается не более 1,5 мм.
Закругленные до радиуса более 4 мм рабочие грани зубцов оттягивают кузнечным способом, нагревая до температуры 820 … 840 °С, и закаливают в воде при 40 … 50 °С на длине 15 … 20 мм от вершины. Крыльчатку и барабаны после ремонта статически и динамически балансируют. Допустимый дисбаланс 10 МН-м.
Матрица гранулятора. Изнашиваются внутренняя поверхность и поверхности отверстий для образования гранул со стороны входа массы травяной муки. Восстанавливают матрицы расточкой на увеличенный размер и гильзованием. Для расточки внутренней поверхности применяют резцы с металло-керамическими пластинками из гексанита Р. Гильзу готовят из стали 20, сверлят отверстия, используя матрицу в качестве кондуктора, а затем гильзу цементуют на глубину 1,2 … 1,5 мм и закаливают до твердости НКС 60 … 62. Гильзу фиксируют в матрице штифтами.
Детали механизмов подачи.
Характерные дефекты: выкраивание и поломка продольных рифов или зубьев вальцов, неисправности транспортеров, износ шестерен, валов и подшипников.
Поломанные продольные рифы, зубья вальцов и гребенки восстанавливают приваркой изготовленных и подогнанных рифов и зубьев.
Ремонт машин и механизмов для раздачи кормов и удаления навоза.
В мобильных машинах, таких, как агрегат типа АПК-Ю для приготовления комбинированных силосов, измельчитель-погрузчик силоса ПСН-1М, кормораздатчик ПТУ-10К, раздатчик-смеситель РС-5А и других, установлены детали, подобные аналогичным деталям рассмотренных машин. Дефекты типовых деталей машин аналогичны, и их восстановление выполняется, как показано в других разделах. При сборке машин и механизмов для раздачи кормов и удаления навоза натяжение цепей регулируют так, чтобы в случае приложения усилия 10 Н в середине пролета цепи ее отклонение было 25 … 40 мм.
В транспортерах ТВК-80А возможны поломки скребков, износ осей звеньев и отверстий в планках, разрывы цепи, соскакивание цепи с натяжкой звездочки из-за удлинения и перекосов оси натяжного вала, изгибы и скручивания валов и др.
Примерные сроки замены основных узлов и деталей транспортера ТСН-3,0Б
Детали | Допустимый износ, мм | Сроки замены деталей, ч |
Поворотная звездочка | 12-14 | 450-500 |
Ведущая звездочка | 5-5,5 | 900-1000 |
Натяжная звездочка | 12-14 | 1500-1800 |
Оси: | ||
Поворотной звездочки | 0,02 | 2200-2500 |
Натяжной звездочки | 0,02 | 3000-3600 |
Тяговая цепь | 4500-5000 | |
Редуктор | 5000-5800 |
Источник
Техническое обслуживание и ремонт машин и оборудования животноводческих ферм проводят с использованием станций технического обслуживания и передвижных мастерских. При выполнении работ по ремонту машин целесообразно использовать стенд ОПР-1058 с набором необходимого инструмента. На этом стенде можно выполнять следующие операции: распиловку и изготовление деревянных деталей, вырезку заготовок из листового материала, электродуговую сварку, заточку режущего инструмента, сверление, резку и гибку труб, получение сжатого воздуха и др.
У этих машин наиболее интенсивно изнашиваются рабочие органы: режущие и противорежущие пластины, дробильные молотки, ножи, решета, деки и др.
Молотковые дробилки. Износ рабочей грани дробильных молотков допускается не более 4 мм по высоте зуба. При износе молотков их переставляют на неизношенную грань.
Перед сборкой молотки, шайбы и оси подбирают по массе для шести комплектов. Разница в массе комплектов, установленных на диаметрально противоположных осях барабана, допускается не более 12 г. При износах отверстий в молотках под оси отверстия развертывают, а оси устанавливают увеличенного размера. По мере притупления острых кромок у отверстий решет до радиуса более 2 мм их необходимо переставлять (четыре положения), используя каждый раз неизношенные. При пробоинах на решето ставят накладку от старого решета, приваривая ее газовой сваркой. После ремонта решето должно иметь правильную форму и при установке заходить в паз с усилием 70…80 Н.
Режущие аппараты. У режущих аппаратов затупляются и повреждаются ножи и противорежущие пластины, ослабляется крепление фланцев на диске, прогибается вал и изнашиваются подшипники, изменяется зазор между ножами и противорежущими пластинами.
Затупившиеся лезвия ножей и противорежущих пластин до толщины кромок более 0,6 мм затачивают до толщины 0,1 мм на абразивном круге при обильном охлаждении. Углы заточки ножей для дробилок типа ДКУ должны быть 24…26° (проверять шаблоном), а у противорежущих пластин 60…61°.
Нож и детали его крепления после заточки устанавливают на прежние места для сохранения балансировки. Между ножом и противорежущей пластиной должен быть зазор 0,5… 1,5 мм, в зависимости от вида перерабатываемого корма. Этот зазор регулируют постановкой прокладок под кронштейны.
У дробилок типа ДКУ нож устанавливают по отношению к плоскости диска под углом 2°, а противорежущую пластину по отношению к горизонтальной плоскости под углом 15° с зазором в 0,3…0,5 мм.
Зазор между режущим барабаном и противорежущей пластинкой в измельчителе кормов «Волгарь-5» должен быть в пределах 0,5… 1,0 мм при разнице его по длине пластины не более 0,2 мм. Для ножей вторичного резания зазор должен быть 0,1…0,5 мм.
У ножей аппарата вторичного резания изнашиваются торец ножа и боковые грани. При толщине более 7 мм торцевые поверхности шлифуют до выведения следов износа. При толщине менее 7 мм на боковые грани ножей по всей длине слоем 1,5…2,0 мм наплавляют газовой сваркой сормайт № 1 и обрабатывают наплавленный слой на плоскошлифовальном станке.
У измельчителей грубых кормов ИКХ-30 изнашиваются и деформируются лопасти, рожки, крыльчатки и зубцы измельчающего аппарата, нарушается его балансировка.
Поврежденные лопасти рихтуют или заменяют. Биение диска допускают не более 1,5 мм, а дисбаланс ротора не более 60 мН∙м (600 гсм).
При закруглении рабочей грани зубцов до радиуса 3…4 мм зубцы оттягивают кузнечным способом, нагревают до 820…840°С и калят в воде (40…50°С) на длине 15…20 мм от вершины. Крыльчатку после ремонта балансируют. Допустимый дисбаланс 10 мН∙м.
Для обеспечения нормальной работы машин проводят статическую и динамическую балансировку барабанов.
У матрицы грануляторов травяной муки изнашиваются внутренняя поверхность и поверхности отверстий для образования гранул со стороны входа массы травяной муки. Восстанавливают матрицы расточкой на увеличенный размер и гильзованием. Для расточки внутренней поверхности применяют резцы с металлокерамическими пластинками из гексанита Р. Гильзу готовят из стали 20, сверлят отверстия, используя матрицу в качестве кондуктора, а затем гильзу цементируют на глубину 1,2… 1,5 мм и закаливают до твердости 60.. .62 HRC. Гильзу фиксируют в матрице штифтами.
Механизм, подачи и передаточный механизм. Характерными дефектами этих механизмов являются выкрашивание и поломка продольных рифов или зубьев вальцов, неисправности транспортеров, износ шестерен, валов и подшипников.
Поломанные продольные рифы, зубья вальцов и гребенки восстанавливают приваркой отдельно изготовленных и подогнанных рифов и зубьев.
Отремонтированные и собранные кормоприготовительные машины вначале проверяют прокручиванием вручную, а затем на холостом ходу с рабочей частотой вращения в течение 4…5 ч и под нагрузкой 2...4 ч.
Паровые котлы и водонагреватели. У котлов парообразователей типа KB появляется накипь на пароподогревателях, жаровых трубах и котлах, в дымовых трубах и коробках отлагаются сажа и зола, отказывает в работе предохранительный клапан и водомерное стекло, появляется пропуск пара в вентилях и соединениях, прогорает колосниковая решетка.
Накипь в котле удаляют химической очисткой с использованием кислот и щелочей или механическим способом. При отложениях карбонатных (СаСо3, MgC03) лучше применять соляную кислоту, а при силикатных — щелочь. Концентрация обычно используемой ингибированной соляной кислоты (ингибитор — уникол) в растворе воды берется в зависимости от толщины слоя накипи. При толщине до 0,5 мм — 2…3%, а при 2,5 мм — 6…8%. Для уменьшения коррозии в кислоту добавляют уротропин, формалин, столярный клей и другие замедлители коррозии в количестве 1,5…2,5 г/л. Продолжительность очистки определяется толщиной слоя накипи, но не более 6…8 ч при 70°С. Удалив раствор, котел промывают чистой водой, а затем в течение 3…4 ч — 1…2%-ным раствором кальцинированной соды, нагревая его до кипения. После этого котел вновь промывают чистой водой.
При удалении накипи щелочью концентрация каустической соды в растворе берется также в зависимости от толщины слоя накипи. При толщине слоя до 0,5 мм — 1…2%, а при 2,5 мм — 5…6%. Раствор в котле кипятят в течение 24 ч, периодически проверяя его концентрацию. При стабилизации раствора кипячение прекращают, раствор сливают, а котел промывают чистой водой.
Для механической очистки котла и труб от накипи применяют в качестве рабочих органов различной конструкции головки, имеющие набор роликов с насечкой (зубцы), сплошные, эллипсоидного типа, а также с насечкой вдоль всей головки. Такие головки закрепляют на гибком валу с приводом от электродвигателя или пневмотурбинки.
Неисправные краны и вентили разбирают и притирают. Водомерное стекло и детали предохранительных клапанов очищают от накипи или заменяют.
После ремонта котлы подвергают гидравлическому испытанию водой под давлением 0,06 МПа. В случае обнаружения течи и пороков в сварных швах их устраняют газовой сваркой, после чего гидравлическое испытание котла повторяют./p>
Источник
Категория:
Практика ремонта машин
Публикация:
Ремонт и регулировка машин для приготовления кормов
Читать далее:
Ремонт и регулировка машин для приготовления кормов
Цель работы.
1. Ознакомиться с характером износа деталей рабочих органов кормоприготовительных машин.
2. Изучить технологию восстановления рабочих органов кормоприготовительных машин.
Задание.
1. Ознакомиться с оснащением рабочего места.
2. Отремонтировать измельчающий аппарат измельчителя кормов ИКС-5.
3. Отремонтировать дробильный и режущий аппараты универсальной дробилки кормов КДУ-2.
4. Отремонтировать аппарат вторичного резания измельчителя «Волгарь-5».
Оснащение рабочего места. Кузнечный горн ОКС-1468-18-040; набор кузнечных инструментов; ванна для охлаждения деталей при закалке в масле и воде ОРГ-3503; штангенциркуль 150 мм; универсально-заточный станок ЗА64Д; стенд ОПР-278 для ремонта и балансировки молотильных барабанов с гидропрессом; токарный станок 1К62; трехгранный драчевый напильник № 1; щуп 1-100 № 5 кл. 2; слесарный молоток; специальная гребенка для проверки расположения и высоты зубьев барабана; пластилин; мел; настольные весы ВНЦ; переносной ацетиленовый генератор ГНВ-1,25; кислородный редуктор РК-53; кислородный баллон А-40, комплект шлангов; горелка «Москва» с наконечниками № 4 и № 5; стальная проволока Св-08 или Св-15, прутки из твердого сплава сормайт-1; защитные очки для газовой сварки ГС-7; стол для газосварочных работ ОКС-1549Б; гидравлический пресс ОКС-ОЗО; плоскошлифовальный станок ЗБ-71М.
Рекламные предложения на основе ваших интересов:
Содержание и порядок выполнения работы. Барабан измельчителя кормов ИКС-5 (рис. 1) после снятия с машины разбирают. Детали барабана моют и дефектуют.
Рис. 1. Барабан измельчителя кормов ИКС-5:
1 — планка; 2 — зуб.
Зубья выбраковывают при износе рабочей грани у вершины до ширины 7 мм, изгибе резьбовой части, срыве двух ниток резьбы, смятии граней конуса.
При меньшем износе рабочую грань зуба оттягивают кузнечным способом, закаливают и подвергают отпуску. Резьбовая часть зуба не калится. После термообработки рабочую грань затачивают. Толщина зуба у вершины должна быть не менее 1,5 мм, длина рабочей части 44—46 мм, угол заточки 45
Биение дисков проверяют в центрах токарного станка. Поверхность изношенного или имеющего забоины конусного отверстия планки обрабатывают напильником так, чтобы конусная часть зуба плотно входила в отверстие. Если кромка, ограничивающая сверху конусную поверхность зуба, мешает плотной посадке зуба, ее спиливают заподлицо с гранями конуса на 3—4 мм по высоте.
Если нижняя кромка конусной части зуба при его посадке в отверстие выступает над внутренней поверхностью планки, под гайку необходимо подложить шайбу 40×40 мм. Толщина шайбы должна быть такой, чтобы она обеспечивала возможность плотной затяжки зуба. Для сохранения статической и динамической уравновешенности такие же шайбы необходимо поставить под гайки диаметрально противоположных зубьев,
У ротора барабана перед установкой зубьев проверяют величину биения посадочных мест вала, расположение дисков относительно оси, прямолинейность поверхности планок.
Биение посадочных мест вала и расположение дисков относительно оси определяют, установив ротор в центрах токарного станка; допустимая величина биения посадочных мест 0,15 мм, торцовое и радиальное биение дисков не должно превышать 1 мм.
Прогиб планок определяют при помощи линейки и щупа. Прогиб планки на всей длине допускается не более 1 мм. При необходимости проводят правку на стенде ОПР-278.
Зубья устанавливают на ротор режущей кромкой в сторону вращения ротора (если смотреть со стороны шкива, барабан вращается против часовой стрелки). Зубья закрепляют двумя гайками. Под гайки устанавливают специальные шайбы. Чтобы обеспечить плотную посадку, при подтягивании гайки необходимо слегка ударять молотком по торцу зуба.
После установки зубьев необходимо проверить их расположение и высоту. Эту операцию выполняют специальной гребенкой. Изогнутые зубья правят. Разница в длине зубьев не должна быть больше 2 мм.
Рабочая частота вращения барабана 2725 об/мин, поэтому после сборки барабан подвергают статической балансировке. Для этого осторожно опускают барабан посадочными местами под подшипники на ролики стенда ОПР-278. Слегка толкнув рукой барабан, сообщают ему вращение. После остановки отмечают мелом самую верхнюю часть барабана. Повторно сообщают барабану вращение. Если отмеченная мелом точка вторично займет верхнее положение, это указывает на то, что дисбаланс расположен в аксиальной плоскости барабана, проходящей через отметку. Если положение отметок при каждом толчке барабана неодинаково, то операцию повторяют 3—5 раз и находят среднюю отметку.
Затем барабан поворачивают так, чтобы плоскость расположения дисбаланса была горизонтальна. Около отметки устанавливают уравновешивающий груз (из пластилина), величину которого подбирают с таким расчетом, чтобы его момент был равен дисбалансу.
Балансировку можно считать законченной, если в любом положении барабан сохраняет состояние равновесия. Если это условие не выдерживается, балансировку повторяют. Контрольную проверку отбалансированного барабана проводят, подвешивая груз (4—5 г) на планку барабана в месте крепления груза.
Рис. 2. Дека измельчающего устройства измельчителя кормов ИК.С-5.
При подвешивании груза барабан должен начать медленно вращаться. После балансировки заменяют пластилин балансировочными шайбами, которые располагают равномерно по всей длине планки.
Деформированную деку (рис. 152) правят и проверяют на плите; прогиб деки (на всей длине) более чем на 1 мм не допускается.
Зубья деки должны быть установлены в корпусе так, чтобы отогнутый конец вершины зуба располагался слева, если смотреть со стороны рукоятки.
Дробильный аппарат универсальной дробилки кормов К Д У – 2. Молотки I дробильного барабана (рис. 3) со ступенчатыми гранями, изношенными на величину более 4 мм, поворачивают для работы неизношенной рабочей поверхностью (рис. 4), точно соблюдая установленную последовательность чередования их и распорных втулок (рис. 5).
После износа четырех рабочих граней дробильные молотки заменяют новыми. Изношенные пальцы (рис. 3) при зазоре между ними и молотком более 1 мм заменяют. Они могут быть изготовлены из стали 50 и должны быть закалены до твердости 40—45 HRC. Диски 3 ротора в случае погнутости рихтуют на плите. Допустимый зазор между диском и поверочной плитой после рихтовки 0,5 мм.
Рис. 3. Дробильный аппарат универсальной дробилки кормов КДУ-2:
1 — молоток; 2 — палец; 3 — диск барабана; 4 — дека; $ — распорная втулка; 6 — диск вентилятора; 7 — лопасть вентилятора; 8 — кожух вентилятора; 9 — вал барабана.
Рис. 4. Схема перестановки молотков дробилки КДУ-2.
Вал барабана со стрелой прогиба более 0,12 мм правят на стенде ОПР-278.
Погнутые лопасти и диск рабочего колеса вентилятора рихтуют на плите. Рабочее колесо вентилятора в сборе должно быть статически отбалансировано. Величина допустимого дисбаланса 26 г-см. Балансировочные грузы должны быть приварены. Собранный ротор барабана без молотков и вентилятора статически балансируют. Допустимый дисбаланс 0,0165 Н-м.
Затем устанавливают пальцы с молотками и распорными втулками. Диаметрально противоположно устанавливаемые комплекты должны отличаться по весу не более чем на 0,1 Н. Комплектовку проводят за счет подбора молотков по весу. Молотки должны свободно поворачиваться вокруг пальцев и иметь осевой зазор 1,5-—2,0 мм.
Рис. 5. Схема расположения молотков ротора дробильного барабана универсальной дробилки кормов КДУ-2 (цифры указывают длину распорных втулок в мм).
Рис. 6. Схема перестановки решет дробильного аппарата дробилки КДУ-2.
Сменные решета при затуплении рабочих кромок отверстий до радиуса 1,5—2 мм поворачивают на 180°. Решета, изношенные с одной стороны, перегибают по радиусу (225 мм) для работы другой стороной (рис. 6).
Чугунные деки дробильного аппарата с рифами, изношенными до высоты 3 мм, заменяют.
В собранном измельчающем устройстве барабан должен свободно от руки вращаться в роликоподшипниках. Осевое биение дисков не должно превышать 0,3 мм. Осевой зазор вала 9 должен быть не более 0,12 мм. Зазор между молотками и деками должен составлять 4—6 мм. Торцовое биение рабочего колеса вентилятора допускается не более 1 мм; колесо не должно касаться кожуха 8.
Режущий аппарат универсальной дробилки кормов КДУ-2. Затупленные до толщины 0,3 мм режущие кромки ножей барабана (рис. 7) и противорежущей пластины (сталь 65Г) затачивают на универсально-заточном станке ЗА64Д. Угол заточки ножей равен 22 противорежущей пластины — 75°. При заточке нельзя допускать понижения твердости закаленных до 45—50 HRC режущих кромок ножей и противорежущей пластины.
После заточки режущая кромка пластины должна быть прямолинейна, отклонение допускается не более 0,3 мм.
Режущие кромки ножей, установленных на барабан, должны лежать на одном и том же расстоянии от оси вращения (142,5 мм). Для этого устанавливают барабан на стенд ОПР-278, закрепляют на стенде противорежущую пластину и регулировочными винтами 8 изменяют положение каждого из ножей относительно пластины.
Рис. 7. Режущий барабан универсальной дробилки кормов КДУ-2:
1 — фрикционные кольца; 2 — ведущий диск; 3 — прижимной диск; 4 — шкив; 6 — пружина; 6 — регулировочные прокладки; 7 — нож; 8 — регулировочный винт.
Допустимое биение кромок лезвий ножей не более 1 мм. Затем проводят статическую балансировку барабана. Допустимый дисбаланс 0,05 Н-м. Балансировочные грузы устанавливают под гайки крепления ножей. После сборки барабан должен свободно от руки вращаться в конических роликоподшипниках, осевой зазор должен находиться в пределах 0,07— 0,15 мм. Конические подшипники регулируют изменением количества прокладок 6 под крышками подшипников.
Предохранительная муфта режущего барабана, если она правильно отрегулирована, передает крутящий момент, равный 60 Н-м. Величину передаваемого крутящего момента проверяют подвешиванием груза 270— 300 Н на радиусе шкива. Если равномерным поджатием пружин 5 нельзя отрегулировать муфту, пружины заменяют.
При уменьшении зазора между торцами прижимного диска и шкива до 0,8 мм фрикционные кольца заменяют новыми. Рабочие поверхности прижимного диска, ведущего диска и шкива протачивают до удаления следов износа.
Нормальный зазор между торцами прижимного шкива и диска должен находиться в пределах 2—2,5 мм.
Рис. 8. Восстановление ножа аппарата вторичного резания измельчителя «Волгарь-5» наплавкой:
1 — слой, наплавленный малоуглеродистой проволокой; 2 — слой твердого сплава сормайт-1.
Аппарат вторичного резания измельчителя «Волгарь-5». Изношенные подвижные и неподвижные ножи аппарата зачищают абразивным кругом до металлического блеска и наплавляют по торцу вдоль всего лезвия электродной проволокой Св-08 или Св-15; толщина наплавленного слоя 2—3 мм (рис. 8). Наплавку ведут кислородно-ацетиленовой горелкой.
Боковые грани лезвия вместе с наплавленным слоем шлифуют до толщины 6 мм и наплавляют сплавом сормайт-1. Для этого на сварочный стол горизонтально кладут нож, нагревают его рабочую поверхность горелкой и наконечником (№ 4 или № 5) до температуры 550—600 °С и наплавляют твердый сплав. Пламя горелки должно быть восстановительным с избытком ацетилена, флюс — плавленая бура. Слой должен быть равномерным по толщине (1,5—2 мм) и сплошным без раковин и трещин.
При необходимости после наплавки ножи правят под прессом, после чего шлифуют на плоскошлифовальном станке до толщины 8—0,08 мм. Во время шлифовки необходимо обеспечить одинаковую толщину слоя твердого сплава на обоих боковых гранях ножей.
Отшлифованные поверхности ножа должны быть плоскими и параллельными. Неплоскостность проверяют щупом толщиной 0,15 на поверочной плите.
Шероховатость отшлифованных поверхностей V Раковины, трещины, отслаивания металла недопустимы.
Отчет о работе. В отчете приводят технологическую карту ремонта одного из узлов рабочих органов (по заданию преподавателя).
Рекламные предложения:
Читать далее: Ремонт погружных электрических насосов
Категория: –
Практика ремонта машин
Главная → Справочник → Статьи → Форум
Источник